Communist to Contemporary Era Yixing History
Listen to the Editorial Conversation for this chapter:
Introduction to the Communist Era
As World War II ended (1945) and Imperial Japanese forces withdrew from China, the Chinese civil war, long simmering below the “United Front"[1], restarted between the Nationalists Kuomintang and the Chinese Communist Party. Mao Zedong’s communist forces were eventually victorious, founding the People's Republic of China in 1949. Chang Kai-shek’s Nationalists retreated to Taiwan.
Yixing production restarted in earnest under the direction of the new communist government in 1955, with the collectivization of the Yixing Zisha Co-op, the predecessor to the Yixing Zisha Craft Factory (江苏省宜兴紫砂工艺厂, Jiangsu Sheng Yixing Zisha Gongyi Chang) – later called Yixing Factory 1 (宜兴一厂, Yixing Yi Chang; “F1”)[2]. The Co-op was merged into Yixing Factory 1 at its founding the following year (1956), with the hiring of 6 master craftsmen to oversee production and teach the artform within the newly collectivized system; these masters-craftsmen were both tasked with the production of their own wares and the education of the next generation of craftsmen. The new centralized production operated as both an extension of the pre-existing apprenticeship system and a new form of collectivization, taking the choice of student out of the hand of the master.
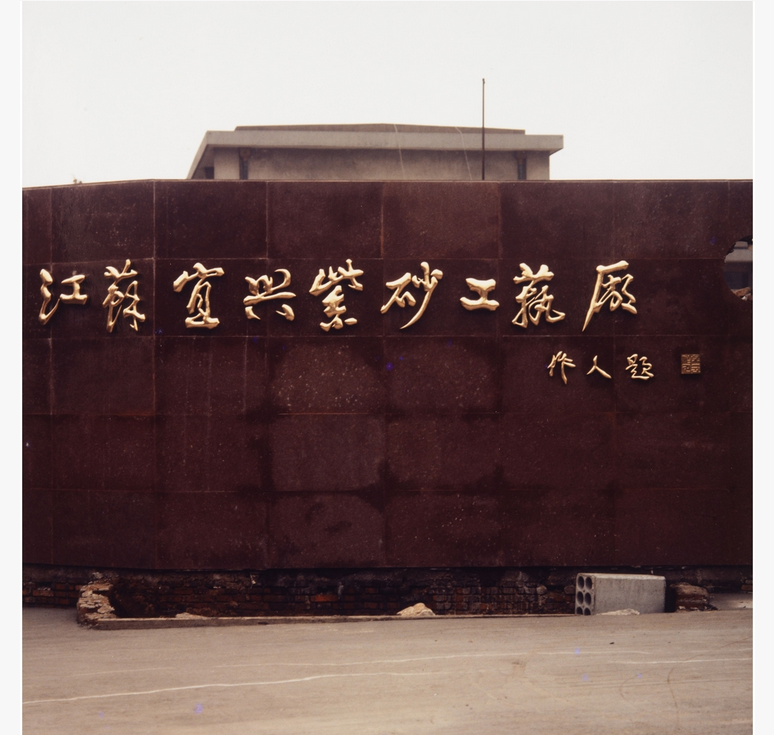
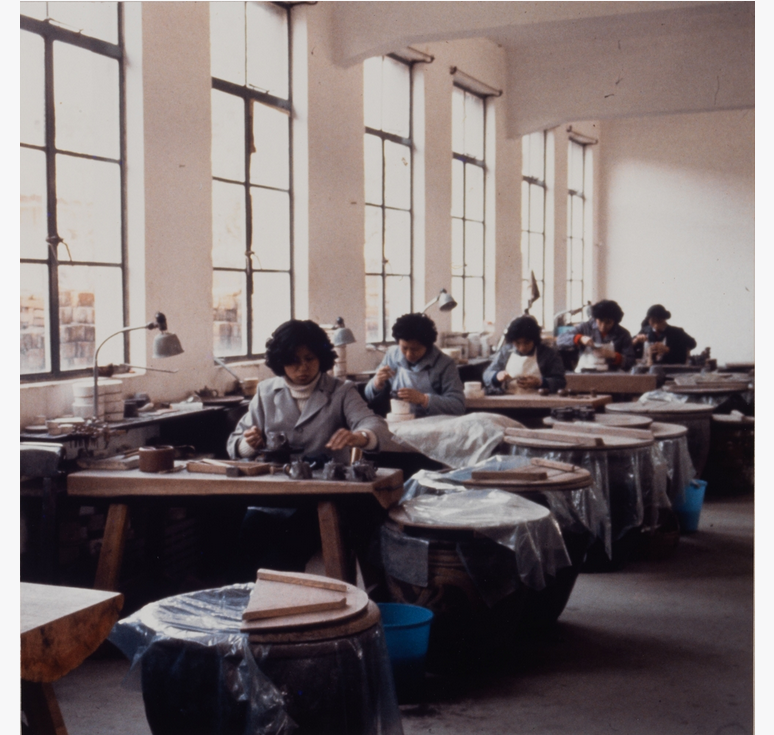
The communist government had a small number of reasons to support the industry, including employment for a skilled workforce capable of generating foreign reserves – Yixing teapots (and other zisha art pieces) of average quality remained in-demand as functional wares amongst foreign buyers and immigrant communities throughout the world, including the United States[3].
The F1 Era is often divided into distinct periods, during which different qualities and styles of teapots were made:
· 1956 – 1965: The Free Period
· 1966 – 1976: The Cultural Revolution Period
· 1976 – early 1980s: The Late F1 Period
Privatization began in the mid-1980s with an influx of Taiwanese business setting up independent factories, and a complete closure of F1 in 1997.
The Free Period (1956 – 1965)
The founding of the institutional factory created a single centralized entity for the creation of all Yixing wares[4]. The early days of F1 oversaw a re-invigoration of the artform after the horrors of the world and civil wars, with the government supplying recognized Yixing masters with students and materials. Yixing was one of the traditional arts which survived from the Dynastic Period through the Cultural Revolution into the present day[5].
During this period, craftsmen were allowed to place their own chop on their work and master craftsmen could produce teapots of their own design; this period most closely resembles the workshop system of higher quality hongs[6].
Six Zisha Ceramic Masters were selected to lead F1 at its founding in 1956:
1. Gu Jingzhou (顾景舟[7], 1915 – 1996), discussed in the previous chapter[8], was the premier Yixing artist of the 1900s, critically acclaimed long before achieving the rank of National Master in 1978.
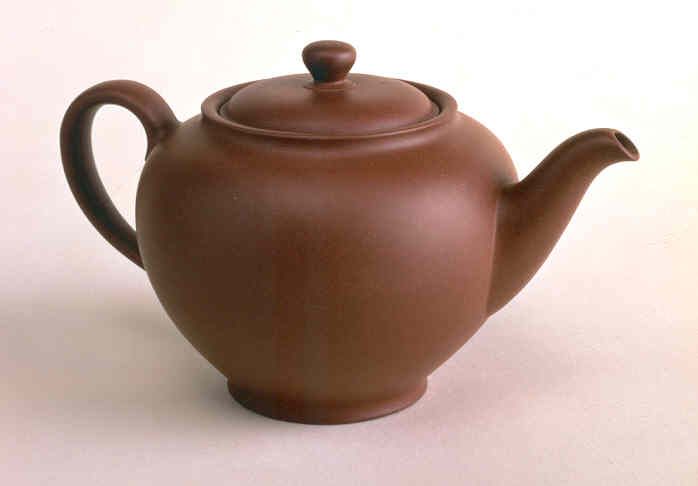
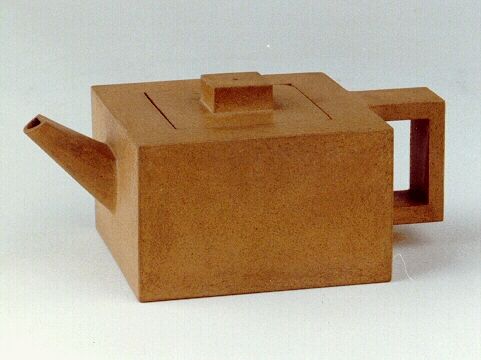
Like many contemporary Master Yixing artists, Gu’s early career was spent forging the works of old masters during the productive years of the RoC era. Gu, adopting the little that remained of literati culture, took multiple artistic names for use on his personal seal throughout his life: His first hao (號/号)[9], during his apprenticeship (in the RoC Era) was 曼晞 (Man Xi), followed by the addition of two characters to his seal, 曼晞陶藝(Man Xi Taoyi, “Manxi ceramics”) after his apprenticeship ended in 1933; this hao was followed by瘦萍 (Shou Ping), and 壺叟(Hu Sou)[10].
2. Wang Yinchun(王寅春, 1897 - 1977) was an eminent Yixing artist of the RoC, known for his complex geometric shapes; during the early RoC, Wang worked side by side with Gu Jingzhou at Tiehua Xuan (铁画轩)[11], and is known to have borrowed the fellow artist’s seal when he misplaced his own. Like many artists of the RoC, he honed his skills producing forgeries of older Yixing masterpieces starting around 1935.
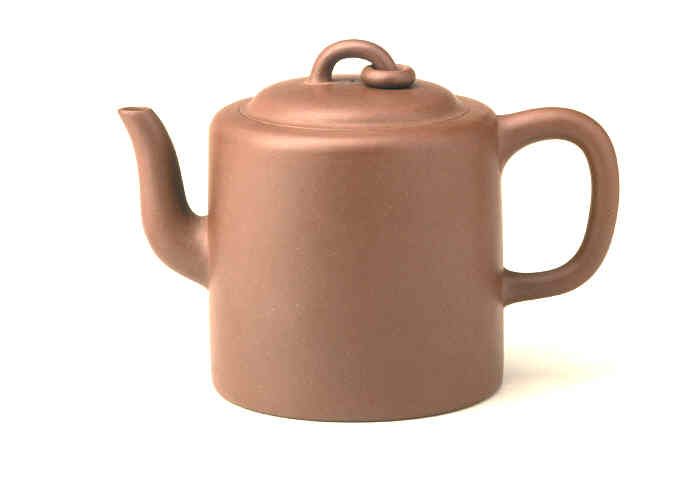
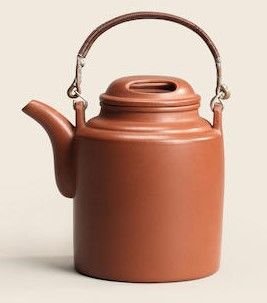
3. Jiang Rong(蔣蓉, 1919 – 2008) was the only woman of the 6 appointed Yixing Masters and the only one to work in the naturalistic tradition throughout the F1 era. Jiang apprenticed with her father (Jiang Hanggao, 蒋宏皋) and uncle (Jiang Yanting, 蒋燕亭), forging naturalistic works of the Qing during the RoC.
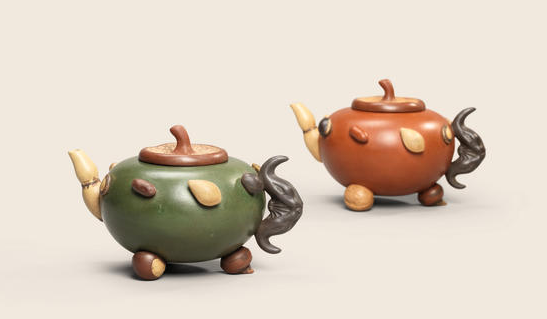
4. Pei Shimin(裴石民, 1892 – 1979 CE) was a celebrated Yixing artist, skilled at producing small objects d’art and teapots in geometric shapes (with the occasional naturalistic production). Pei’s involvement in F1 was reduced after the Cultural Revolution.
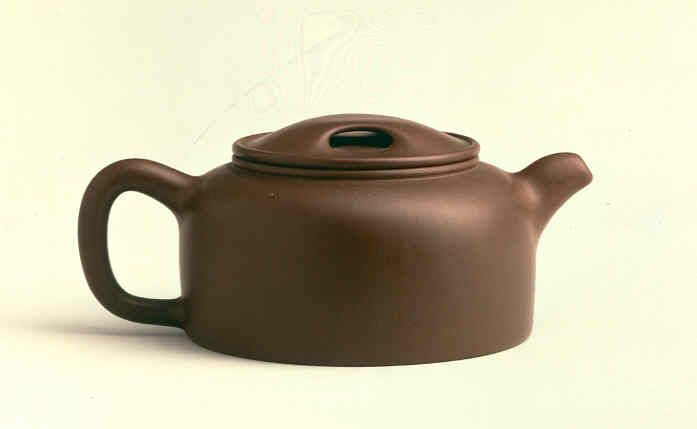
5. Zhu Kexin(朱可心, 1904 – 1986 CE) was a founding teacher (1930) at the Jiangsu Pottery Industrial School, the predecessor to F1. Zhu produced complex and unique shapes of Yixing teapots during the RoC and early F1 period; his involvement in F1 was diminished during the Cultural Revolution.
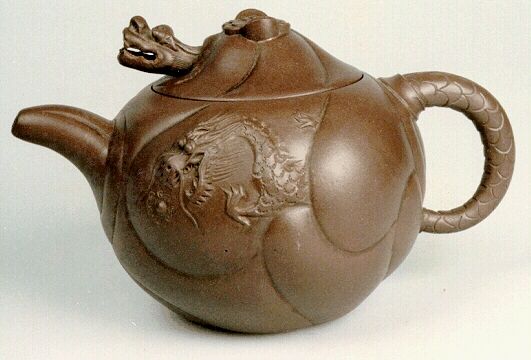
6. Ren Ganting[14] (任淦庭, 1889 – 1968 CE) was the only zisha inscriber of the 6 Masters, known for calligraphy and line-drawings[15]. Ganting apprenticed to Lu Lanfang (卢兰芳, 1870-1930) starting at 15 years old and worked at the Wu Desheng Hong (吴德盛) during the RoC. His inscriptions include fine landscape and naturalistic motifs as well as folk-art influences.
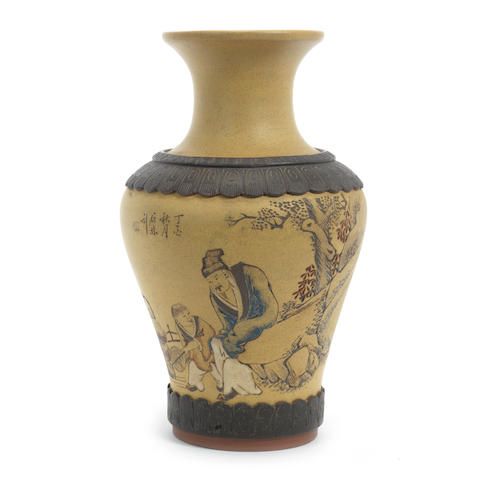
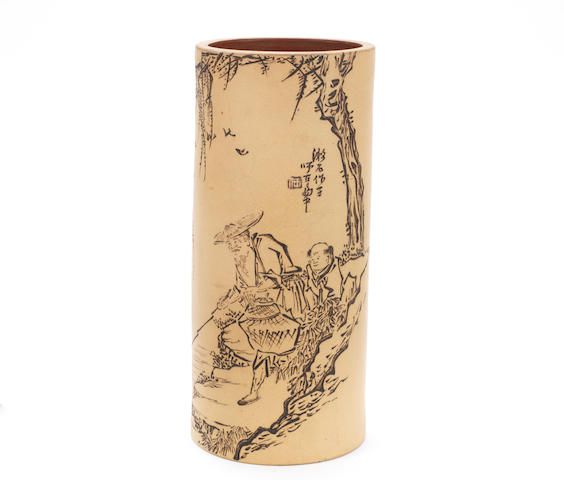
Wu Zhilai[16] (吴芝莱, 1892 – 1969 CE), the top apprentice to Zhu Kexin (朱可心, 1904 – 1986 CE) during the RoC, is often listed as a seventh founding Master Craftsmen of F1. Wu is known for elegant square shape teapots with rounded sides, based on ancient wine-pots, and for teapots with naturalistic designs and overhead handles. Wu, alongside other masters on this list, produced work for Tiehua Xuan (铁画轩) during the RoC. He is sometimes edited out of the official history, as he committed suicide after being disgraced by the Red Guards during the Cultural Revolution.
The six Master Craftsmen were assigned apprentices, ranked according to a new system mandated by the Party, who were to be taught all aspects of Yixing production, including clay processing, ceramic skills, and firing. By 1958 there were approximately ~2,000 individuals working within the F1 factory.
By the end of the Free Period, the state had begun to mandate specific designs to be made enmasse, marketing the wares in catalogues of approved designs; the majority of these wares were made by lesser-ranked craftsmen within the factory system.
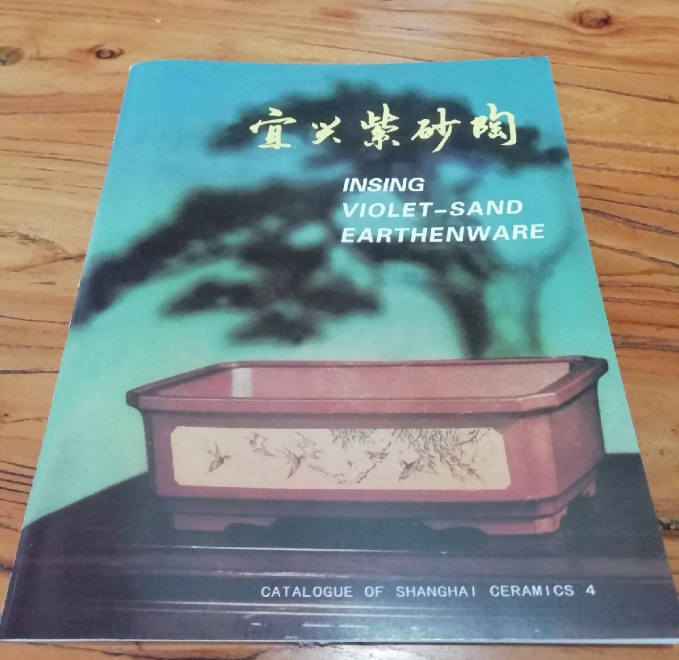
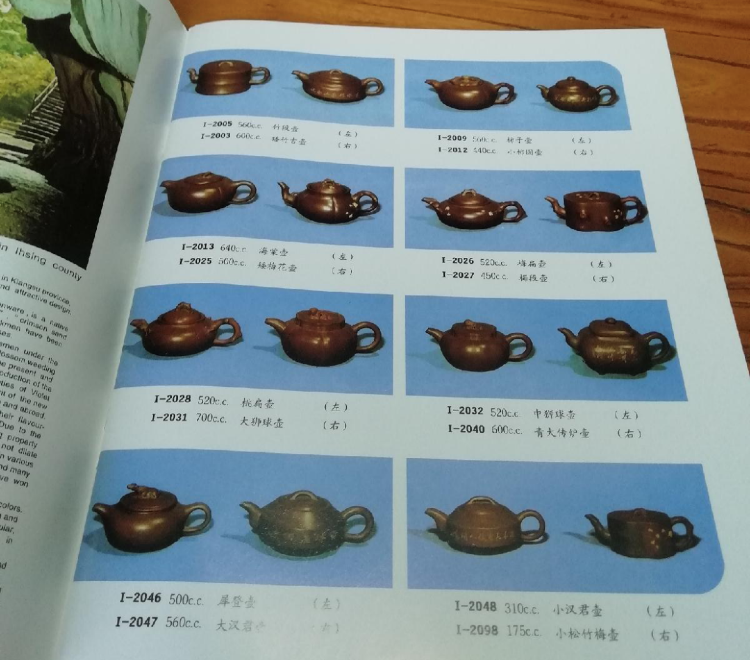
The Cultural Revolution Period (1966 – 1976)
The Cultural Revolution (1966 – 1976, 文化大革命) was both a social and political movement, dually aimed at eradicating traditional culture seen as anti-communist and restoring Mao Zedong to a position of power[17]. Mao proclaimed professionals (doctors, lawyers, and others) and the literati as class enemies seeking to undermine the party and revolution; the Cultural Revolution empowered self-proclaimed Red Guards to ideologically police and persecute individuals seen as counter revolutionary or bourgeois under the banner of destroying the Four Olds (四旧, Si Jiu): “Old Ideas, Old Culture, Old Customs, and Old Habits”. Historical Sites, cultural artifacts, personal collections, paintings, ceramics, furnishings, and historic-architecture, in both public and private hands, were all targeted for destruction by the Red Guards, often arbitrarily and without regard to historical significance or cultural value. Teaware was not spared.
The F1 factory was further collectivized, with masters, apprentices, and craftsmen divided into brigades, the best known of which are: Hongyu (红雨), Shisheng (石生), Qitao (跂陶; “pottery”). Communist ideology held that individuals should glorify the commune and state, working without individual recognition; prohibitions on self-aggrandizement were brutally enforced by the Red Guards: the ceramic masters were no longer allowed to place their chops on individual teapots and thus worked without differentiation[18] – all wares, made by master or entry-level craftsman alike, were signed “中国宜兴” (Zhongguo Yixing, “China Yixing”). The prohibition on individual signatures lasted until the end of the Cultural Revolution, in approximately 1975.
Throughout the Cultural Revolution period, Red Guards entered the F1 factory and destroyed many older works held as reference and tormented the master craftsmen. Zhu Kexin (朱可心, 1904 – 1986 CE) was placed under house arrest, Wu Zhilai (吴芝莱, 1892 – 1969 CE) committed suicide after torture by the Red Guards, and Jiang Rong was accused by the Red Guards “Youth Corps” of working with the Nationalist (KMT) government before the revolution; she was banned from making Yixing wares and sentenced to 10 years (1966 – 1975) of hard labor within the F1 factory.
Yixing teapots, once an art of the bourgeois literati, were adapted and reinterpreted during the Communist era into a ware for the masses, symbolizing the triumph of collectivization and of Chinese socialism. Many teapots were produced featuring the hammer and sickle or revolutionary phrases.
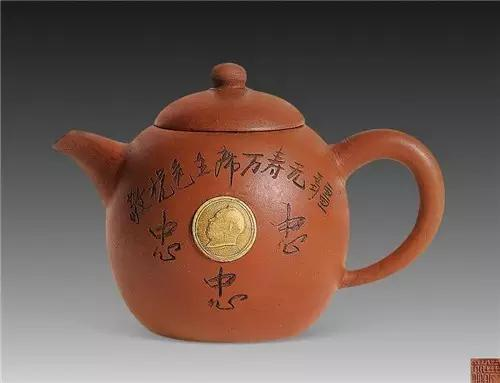
The production of Yixing teapots expanded during the Cultural Revolution period with growing production of mass market lower quality wares. To supply the expanding production demands, Yixing ore mining[19] became drastically more mechanized and industrial with the transition from open pit mines to modern shaft mines starting in 1958 and mine electrification in 1959. The transition to shaft mines, and the use of dynamite in their construction, allowed for much deeper mines; the original mines were generally surface layer to ~5 meters deep; the deepest mine, Shaft Mine #4 started in 1972, eventually reached 800 meters deep.
The communist government had all craftsmen subjected to tests of skill, rewarding titles by seniority and ability: Assistant Master Craftsmen (助理工艺师, Zhuli Gongyishi), Master Craftsmen (工艺师, Gongyishi), Senior Master Craftsmen (高级工艺师, Gaoji Gongyishi), and National Grand Master Craftsmen (国家级工艺美术大师, Guojia Ji Gongyu Meishu Dashi). Before the Cultural Revolution, the senior ranks of Master Craftsmen had access to superior quality clay; during the Cultural Revolution, all teapots produced by F1 used various clays processed in bulk (such as zini[20], for example) – the Master Craftsmen used the same clay as their apprentices and mere-craftsmen. Just as with the industrialization of Yixing zisha mines, the processing of clay[21] was mechanized with milling machines[22] and industrial mixers throughout the Cultural Revolution Period to support the increased production quotas.
Finally, in parallel to the industrialization of mining and clay processing, the techniques of firing were likewise mechanized[23]. F1 transitioned away from wood fired Dragon kilns as early as its founding, experimenting with various forms of downdraft kilns in the 1960s, before settling on tunnel kilns by 1973.
In the latter half of the Cultural Revolution period and into the Late F1 Period, Yixing teapots were produced at three indistinct levels of craftsmanship:
- Works by Master Craftsmen: non-commercial production for the state, shown at exhibitions or given as gifts to dignitaries and ambassadors.
- Works by apprentices: commercial production made in large quantities for export; these works generally went to higher-priced markets such as the United States and Japan.
- Works by craftsmen: mass-market mass-production work for domestic sales and export to lower-priced countries such as Malaysia and Thailand.
Though production of Yixing teapots increased during the Cultural Revolution period, the low quality and decline in domestic consumption suppressed the price of Yixing wares; records indicate that many craftsmen-made teapots were sold for 20 cents apiece.
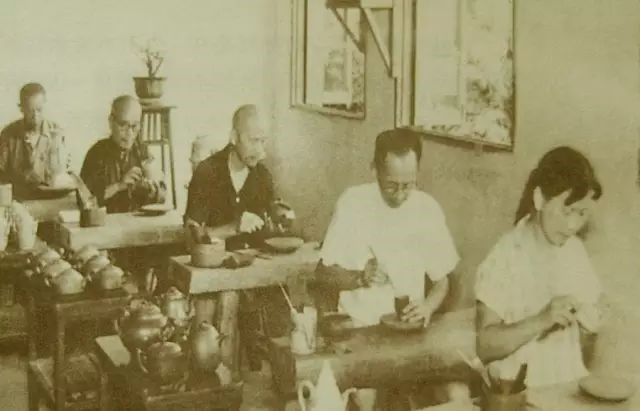
The Late F1 Period (1976 – mid-1980s)
Conditions began to improve with Mao Zedong’s death and the end of the Cultural Revolution. China’s new leader, Deng Xiaoping, began a process of opening and reform which led to economic growth and a new foundation for industry. The reopening of China led to the revival of ceramic arts in Yixing, partially attributable to one Individual – K.S. Lo.
Lo, the retired CEO of Vita Soy in Hong Kong, became interested in antique Yixing teapots in the early 1970s and first visited Yixing in Autumn 1979, where he was dismayed by the quality of workmanship, finding only mass-produced teapots stamped with the 4-character 中国宜兴chop. After much discussion with the ceramic artists, he determined that quality craftsmanship was disregarded[24] because they believed (likely correctly) that there was no market for better, more expensive, wares. With an aim to revitalize the art of Yixing, Lo attempted to commission teapots of his own design, in the tradition of the Qing dynasty literati; the order was rebuffed by the factory as they had a quota of production from standardized designs in the F1 Catalogue. Lo eventually received permission to place the custom order from the China Arts & Crafts Import & Export Corporation in Nanjing[25] in late 1979; the terms of the commission had Lo’s new company, Sheung Yu Ceramics Art Limited, pay for the estimated yearly output of 20 higher-rank ceramic artists. The commission designs were based on older masterpieces and followed the dynastic and RoC traditions of Yixing – a single teapot, made by a single artist, with the artists chop identifying authorship; the commission was delivered two years later, in 1981, a year longer than expected[26]. The newly commissioned teapots were exhibited side by side with Lo’s collection of antique Yixing wares, invigorating interest in the industry within Hong Kong and the greater Chinese and Asian overseas communities. Additional exhibitions were held in Taiwan and abroad.
Exceedingly few ceramic artists were promoted in rank during the Cultural Revolution period, such that by 1979 Yixing Factory 1 employed ~600 craftsmen, clay processors, and ore minors, all overseen by only less than 10 master craftsmen.
The ceramic artist rankings were updated in the late-1970s[27], at the end of the cultural revolution period:
- Technician[28] (技术员, Jishuyuan)
- Craftsman (工艺美术员, Gongyi Meishuyuan)
- Assistant Master Craftsman (助理工艺师 (Zhuli Gongyishi)
- Master Craftsman (工艺美术师 (Gongyi Meishushi)
- Senior Master Craftsman (高级工艺美术师 (Gaoji Gongyi Meishushi)
- Senior Research Master Craftsman (研究级高级工艺美术师, Yanjiuji Gaoji Gongyi Meishushi)[29]
Starting in the Late F1 period, Yixing teapots made for export were intermittently sold with a sticker, leading to a system of dating based on the specific attributes of the label; while this system originally worked as intended, the stickers are easily copied and have become a common source of contemporary fraud. The presence of a sticker should not be trusted as an identifying attribute without other confirmatory evidence of age.
The first sticker used during the Late F1 Period was the Oval Green Label from 1977 – 1983 CE[30], a green oval sticker with the English words “Made in China” printed in gold; the label was slightly shiny and easily abraded. The oval green label marks the reintroduction of creative designs from F1.
No labels were used (the “No Label Period”) from 1983 – 1986.
Stickers returned to F1 export teapots with the Diamond Label from 1986[31] – 1992. The label had many overlapping variations in material and design over time; the text on the label reads: “方圆牌” (Fang Yuan Brand) and "Yixing China 紫砂” (Zisha), while the label material varied, starting in paper with white text (without plastic film) from 1987 – 1988, followed by a laminated version[32]; followed by colored variations with gold text, silver text, and shiny white. The design of the label has variations with and without a separating white line cutting the diamond in half. One final label was used by F1, the Laser Round Label, from 1993 – 1997; the sticker is holographic and difficult to remove.
End of F1 into the Contemporary Period
The F1 Era ended not with a bang, but a whimper. The economic reforms of China opened the door for personal crafts and private enterprising – Yixing ceramic artists of F1 were allowed to produce and sell wares of their own creation after fulfilling their production quotas, and the first private Yixing studio since the RoC was founded in Yixing town. Yixing Zisha Factory 2 (sometimes referred to as F2)[33] was established in 1984 by two master Craftsmen of F1, brothers Xu Hantang (徐汉棠, b. 1932) and Xu Xiutang (徐秀棠, b. 1937), alongside a few employed ceramic artists and craftsmen previously at F1. Yixing Factory 2 was followed by Yixing Factory 3, 4, and 5[34]; Factories 3 and 4 generally produced flowerpots and other large pieces, while Factories 2 and 5 produced teapots with, as an overgeneralization, less skill in craftsmanship.
There is debate as to the quality of clay in this late period; while some claim that F1 maintained exclusive access to the best quality clay until its prolonged demise in 1992 (with the deconstruction of its kiln)[35], others claim that private investment in F2 and F5 allowed the competing factories to source superior clay for rich markets such as Hong Kong and Taiwan[36]. In actuality, clay tampering[37] became increasingly common (in F1 and the other factories) in the 1980s and exceedingly common in the 1990s – additives such as barium carbonate, manganese oxide, and iron oxide were used to achieve textural or coloration effects with low regard for purity and safety. The teapots of this era, with few exceptions, are not generally sought after by higher level practitioners.
With the opening of China to international markets and the renewed interest in Yixing wares, investors began the mass purchase of earlier F1 production (and the occasional antiques); the market rate for Yixing ceramics rose drastically with purchasers from Taiwan and elsewhere viewing the ceramic collectables as investment pieces[38]. Just as in the past, the nascent drive present throughout the dynastic period and the RoC reemerged with privatization – ceramic artists, seeking their fortunes, began the mass-forgeries of antique wares for the Taiwanese market. These fakes still circulate on the market today.
With the decline and end of F1, the rise of private enterprise, and a renewed interest in zisha ceramic arts, Yixing entered and thrived in a new era; by 1994 there were more than ~20+ private Yixing studios, employing more than 1,000 Yixing ceramic artists. While problems of forgeries, low quality production, and tampered clay persist into the present day – the art of Yixing survives with high quality contemporary production available for a price.
Yixing and the tradition of Yixing Ceramics was not eradicated during the Cultural Revolution era or broader communist period; the period was one of dichotomies in tension: the artform was restricted and taught to new apprentices, the mines were expanded and the ore blended, the craftsmanship declined and skills were refined. Yixing was changed by the changes in society that shaped the originating culture – Yixing is not and has never been separate from the history of China, and the history of China, Dynastic, Modern, and Contemporary continue to shape the future of Yixing.
[1]Technically the Second United Front: an uneasy and very temporary alliance between the KMT and CCP for defending China from Japan.
[2]The term “F1”, short for Yixing Factory 1, arose much later, after the founding of Yixing Factory No 2 in the 1980s.
[3]The USA maintained a minor tea drinking culture which survived the transition to coffee during the Revolutionary War against the tea-drinking and-taxing British.
[4]Rumors abound about non-F1 wares from its founding to the 1980s; suffice it to say that Communist China, especially during the Great Leap Forward and the Cultural Revolution, was not the time for private enterprising or attempts at personal enrichment. The Great Leap Forward (1958 – 1962, 大跃进) was a failed campaign aimed at modernization which led to the mass starvation of up to 55 million people and The Red Guards of the Cultural Revolution (1966 – 1976, 文化大革命) denounced and killed individuals suspected of being insufficiently ideologically aligned with party doctrine (the death toll varies from hundreds-of-thousands to millions of individuals). Ceramic Artists had more to fear from minor infringements of doctrine than any desire to make personal wares on the side.
[5]Alongside the production of tea.
[6]A system of ceramic studios discussed in the previous chapter An Abbreviated History of Yixing Teapots: Republic of China Yixing History.
[7]景舟is Gu’s artist name by which he is best known; his given name is pronounced the same with different characters (景洲, Jing Zhou).
[8]Ibid.
[9]hao: a self-given name for publications and art, very common practice amongst the literati, and often changed throughout life to reflect maturation or discontinuity in art and interests.
[10]A few other haos were used for a short time, debate continues on which additional chops are Gu's and pair with specific periods.
[11]A Hong discussed in the Previous Chapter: Ibid.
[12]Note that Wang Yinchun is known to have used Gu Jingzhou’s seal on some pots made during the RoC; both ceramic artists produced wares of the highest craftsmanship, and determining provenance of their real teapots with mismatched seals is very challenging.
[13]See discussion of Qianlong era version in previous chapter An Abbreviated History of Yixing Teapots: Qing Dynasty Yixing History.
[14]Also known by his courtesy name (字, “zi”, formerly in China used by individuals above 20 years old to refer to peers of the same generation): Foushuo (缶硕), and artistic name (號/号, “hao”, self-given name for publications and art, a very common practice amongst the literati, and often changed throughout life to reflect maturation or discontinuity in art and interests): 漱石 (Shushi), 石溪 (Shixi), 聾人 (Longren), 大聾 (Dalong), 左民 (Zuowan), and 左腕道人 (Zuowan Daoren).
[15]Ganting thus made few Yixing wares of his own.
[16]Given name Wu Yungen (吴云根).
[17]One of these goals being subservient to the central goal.
[18]It is claimed that the Brigade signature can be found under the lid on some teapots; I have not verified this and am actively looking for confirmatory evidence.
[19]A full treatment on Yixing mining is discussed in later chapter: The Mines of Yixing.
[20]There are legitimate debates and opinions on variations in the quality of zisha clay produced over various periods of F1.
[21]A full treatment on Yixing zisha processing is discussed in later chapter: From Yixing Ore to Zisha Clay.
[22]Introduced as early as 1958; while some clay made from the new machines was used in the Free Period, it is likely that most clay wasn’t machine processed until the late Free Period or Early Cultural Revolution Period, as there is a lag between the introduction and the use of the clay, as the processed clay needs to age before use.
[23]A full treatment on Yixing zisha firing is discussed in later chapter: Firing of Yixing Clay.
[24]With the exception of work made for the state by top ranked Master Craftsmen.
[25]The factory originally had to “sell” all wares to an export company under the communist system; K.S. Lo was the first individual to place a direct order with F1.
[26]It took the artist twice as long as expected to fill the order.
[27]And ceramic artists were once again allowed to place their chop on their production, starting in 1978.
[28]An individual employed in ore refinement or kiln-firing; not a ceramic artist.
[29]Often referred to as 研高 (Yan Gao); Gu Jingzhou was promoted to this rank in 1978.
[30]All dates are approximating, generally within 1 year. The specific dates and attributes remain a source of unproductive debate, in my opinion.
[31]Possibly started a year later, in 1987.
[32]The laminated plastic often falls off with age; many real laminated stickers are missing their plastic overcoat and can be identified by matte paper vs gloss paper.
[33]The name is deceptive – with the exception of F1, none of the other factories were under State control.
[34]Yixing Factory 5 was founded by Taiwanese investors.
[35]The shell of F1 limped along until about 2000 CE.
[36]Nearly all private production of Yixing in the 1980s and 1990s were export only, produced for Hong Kong, Singapore, Taiwan, Malaysia and other SE Asian countries.
[37]Discussed in detail in subsequent chapter: Yixing Zisha Ore: Undesirable Additives Used in Zisha Clay.
[38]This is sometimes described as a bubble, though the Yixing bubble never quite “popped”.